What is Porosity in Welding: Key Elements and Their Effect On Weld High Quality
What is Porosity in Welding: Key Elements and Their Effect On Weld High Quality
Blog Article
The Scientific Research Behind Porosity: A Comprehensive Guide for Welders and Fabricators
Understanding the intricate devices behind porosity in welding is important for welders and makers striving for flawless craftsmanship. As metalworkers explore the depths of this phenomenon, they uncover a globe governed by numerous aspects that affect the formation of these tiny spaces within welds. From the structure of the base materials to the complexities of the welding procedure itself, a wide variety of variables conspire to either worsen or minimize the presence of porosity. In this detailed guide, we will certainly decipher the scientific research behind porosity, discovering its effects on weld high quality and introduction advanced techniques for its control. Join us on this journey with the microcosm of welding imperfections, where accuracy fulfills understanding in the search of perfect welds.
Comprehending Porosity in Welding
FIRST SENTENCE:
Assessment of porosity in welding discloses crucial insights into the integrity and quality of the weld joint. Porosity, identified by the visibility of cavities or voids within the weld metal, is an usual worry in welding processes. These gaps, otherwise appropriately addressed, can endanger the architectural integrity and mechanical buildings of the weld, bring about prospective failures in the completed product.
To spot and measure porosity, non-destructive testing techniques such as ultrasonic screening or X-ray inspection are commonly used. These strategies allow for the identification of interior defects without compromising the integrity of the weld. By examining the size, form, and distribution of porosity within a weld, welders can make educated choices to enhance their welding procedures and achieve sounder weld joints.
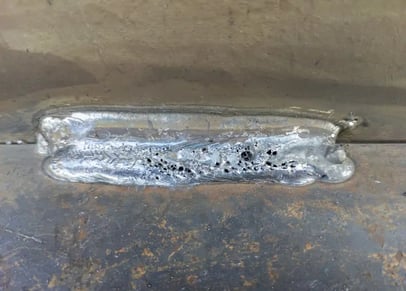
Variables Affecting Porosity Formation
The occurrence of porosity in welding is influenced by a myriad of elements, ranging from gas protecting effectiveness to the complexities of welding criterion setups. Welding criteria, including voltage, existing, take a trip rate, and electrode type, additionally effect porosity formation. The welding method employed, such as gas metal arc welding (GMAW) or protected metal arc welding (SMAW), can affect porosity formation due to variants in warmth circulation and gas insurance coverage - What is Porosity.
Impacts of Porosity on Weld Top Quality
Porosity development significantly jeopardizes the architectural stability and mechanical homes of welded joints. When porosity exists in a weld, it develops voids or dental caries within the product, lowering the general stamina of the joint. These spaces act as stress focus factors, making the weld much more vulnerable to splitting and failure under lots. The existence of porosity additionally deteriorates the weld's resistance to corrosion, as the caught air or gases within deep spaces can respond with the surrounding environment, bring about deterioration in time. Additionally, porosity can prevent the weld's capacity to hold up against stress or effect, more threatening the overall quality and reliability of the bonded framework. In critical applications such as aerospace, automotive, or architectural buildings, where safety and security visit this web-site and resilience are critical, the detrimental impacts of porosity on weld top quality can have extreme repercussions, stressing the relevance of lessening porosity through appropriate welding strategies and procedures.
Strategies to Lessen Porosity
To improve the high quality of welded joints and make sure architectural integrity, welders and fabricators employ details techniques intended at lowering the formation of gaps and cavities within the material throughout the welding procedure. One effective technique to minimize porosity is to ensure appropriate material prep work. This consists of thorough cleaning of the base steel to get rid of any type of contaminants such as oil, grease, or wetness that can add to porosity formation. Additionally, making use of the suitable welding criteria, such as the correct voltage, present, and travel speed, is important in protecting against porosity. Maintaining a constant arc size and angle throughout welding likewise helps in reducing the possibility of porosity.

Using the suitable welding method, such as back-stepping or using a weaving motion, can likewise help distribute heat equally and minimize the possibilities of porosity formation. By carrying out these strategies, welders can effectively lessen porosity and produce premium bonded joints.

Advanced Solutions for Porosity Control
Implementing advanced technologies and cutting-edge techniques plays a pivotal duty in accomplishing superior control over porosity in welding procedures. One sophisticated option is using sophisticated gas combinations. Securing gases like helium or a combination of argon and hydrogen can help minimize porosity by providing far better arc stability and improved visit the site gas coverage. Additionally, employing innovative welding strategies such as pulsed MIG welding or changed atmosphere welding can likewise aid reduce porosity concerns.
One more advanced solution entails using advanced welding devices. As an example, using equipment with integrated functions like waveform control and sophisticated source of power can boost weld top quality and lower porosity threats. The implementation of automated welding systems with precise control over criteria can considerably lessen porosity flaws.
In addition, integrating advanced monitoring and examination modern technologies such as real-time go to these guys X-ray imaging or automated ultrasonic testing can assist in spotting porosity early in the welding process, permitting immediate restorative activities. Overall, integrating these advanced options can significantly improve porosity control and improve the overall quality of welded parts.
Final Thought
In verdict, recognizing the scientific research behind porosity in welding is necessary for welders and producers to produce premium welds - What is Porosity. Advanced remedies for porosity control can additionally enhance the welding procedure and guarantee a strong and trusted weld.
Report this page